Productivity of the U.S. Housing Industry
How has productivity in the U.S.'s housing industry changed in recent years and how will that shape future market tendencies?
Since the housing crisis in 2007, the U.S. was thrust into a deficit of available housing. As of late 2020, that shortage of available housing and housing demand was around 3.8 million and growing1. Supply chain issues as well as labor shortages in the aftermath of the COVID-19 pandemic require builders to be much more creative and productive with the resources they have at hand.
Considering the widening deficit between housing demand and housing supply, a shortage of labor, and a shortage of materials due to supply chain issues, how has the residential construction industry adapted to maximize productivity out of its labor and material resources? On one hand, there are noticeable shifts in material use which offer flexible alternatives to conventional materials. Furthermore, there are changes in design preferences to maximize productivity from limited material resources. However, a major weakness is in labor, historically a lagging factor which exposes builders to long term financial commitments and restricts their flexibility during rapid up turns in production.
Housing in the United States is overwhelmingly built using “stick frame” designs. In these homes, lumber is the overwhelming structural component for walls, floors, and roofs. Therefore, these designs are heavily impacted by fluctuations in lumber supply and price. The largest global exporter of softwood lumber used in construction is Canada, with almost 25% of the global market share2 and 86.7% of US lumber imports. The Trump administration’s 20% tariff against lumber combined with Covid related supply chain disruptions at logging sites, lumber yards, sawmills, and ports of entry caused lumber import prices to spike over 360% between June 2019 and June 20213. (Figure 1)
One mark of shifts in US housing production is changes in new house materials. Particularly a shift from traditional wood framing/stick-built houses to concrete. The South in particular seems to be driving demand in this area with a strong regional emphasis on concrete framing. One could argue the declining share of stick-built homes to be attributable to tariffs against Canadian lumber under the Trump administration, but the trend appears first in 2014 and continues after repeals of said tariffs by the Biden administration. This is likely indicating other factors in new-built single-family homes for sale. One key market difference is new homes built for sale versus by contractor or owner. Over 78% of all new homes completed in 2021 were built for sale. Of these homes, 11% were built using concrete framing in 2019, up from a low of 5% 10 years earlier4. In fact, there has been a growing trend toward concrete framing since 2014 (Table 1). Particularly in one of the busiest housing markets in the country, the South. Additionally, rising prices for lumber have resulted in many builders shifting to concrete or steel framing in place of scarce lumber.
Due to these supply constraints and rising prices, a tremendous gap began to form between housing starts and completions (Figure 2). Lead times began to increase as manufactured material resources such as lumber and manufactured goods such as appliances, windows, and wiring became scarcer5. However, home starts and completions both rose between 2019 and 2021. A key area of productivity improvement came from changing building trends and methods such as switching from the predominant single-family detached homes to attached multifamily housing.
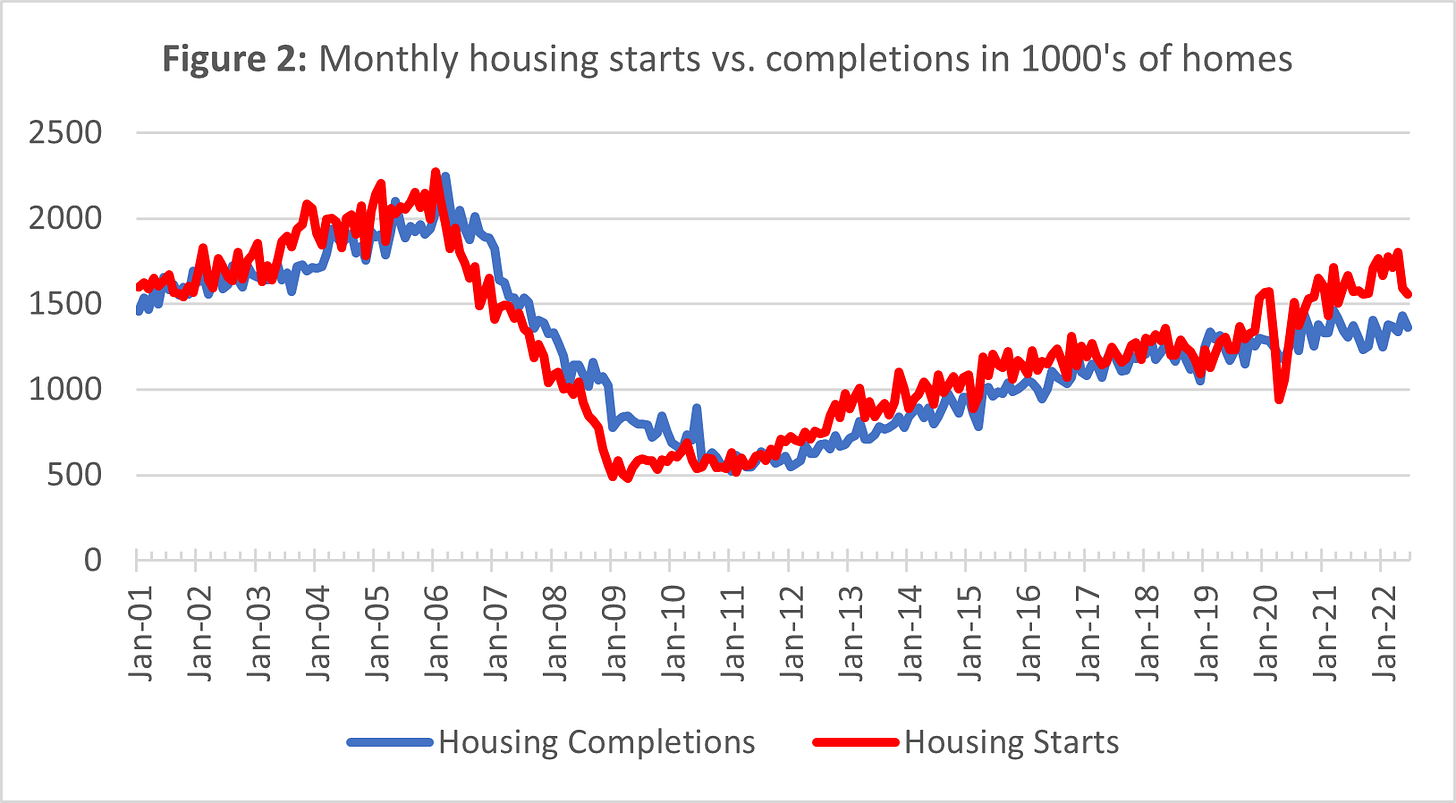
Multifamily structures such as townhomes, condos, and apartment buildings use shared structural features such as exterior walls and foundations to reduce the required material per unit of housing. For instance, three detached single-family homes with the exact same floor plan will require structural and exterior material for all three front faces, all three back faces, and SIX side faces. Turning these into attached townhomes where the middle unit connects to both units on its sides cuts out TWO structural walls and FOUR exterior/decorative faces. The material and unit cost advantages this provides to multifamily therefore makes it a more productive model of development capable of producing many units of housing for less per individual residence. As a result, multifamily buildings took a larger share of total housing production in the aftermath of the 2007/2008 housing crisis, though still not disrupting single-family’s dominance. (Figure 3)
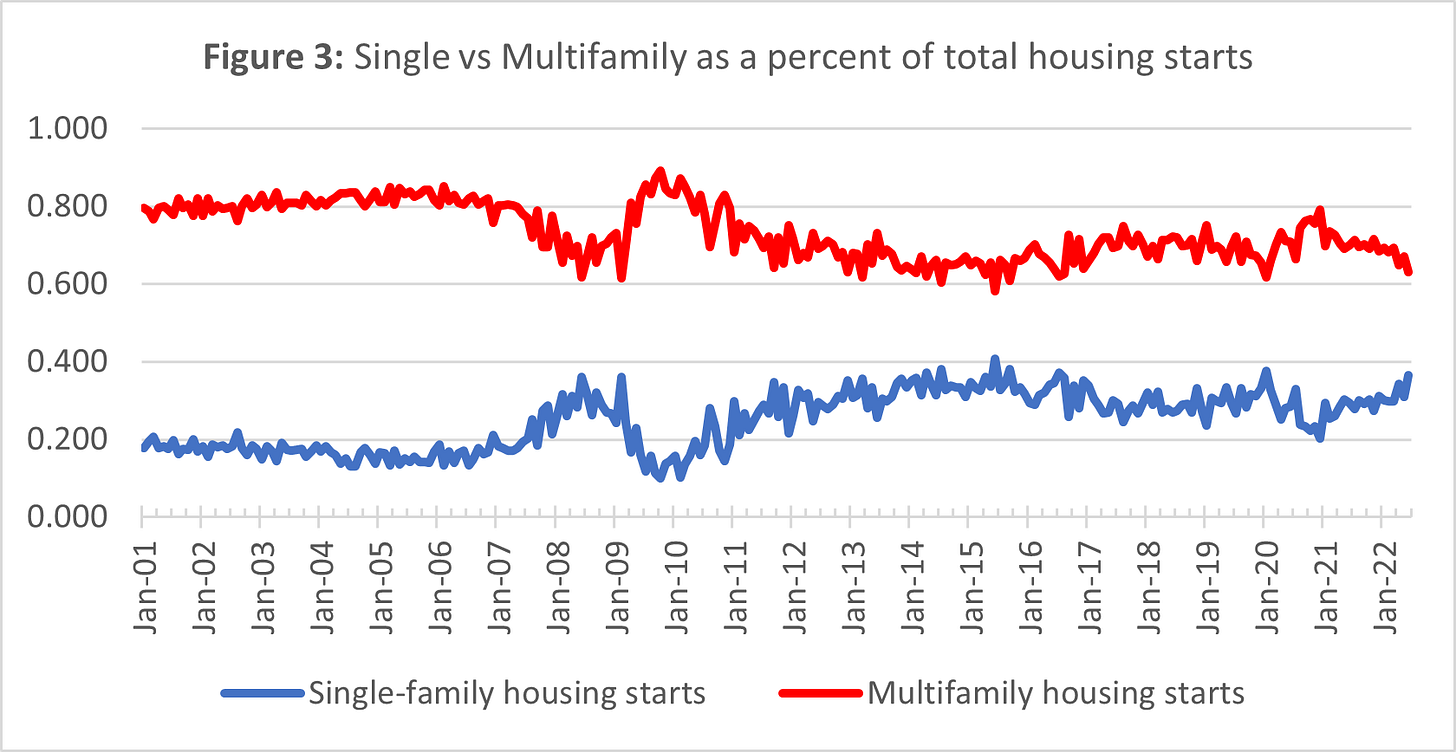
During the height of the Covid-19 pandemic in 2020 and 2021, a shortage in available labor became another factor for construction companies. Despite increasing starts of buildings, the labor market could not keep pace. From 2011 to 2021, the residential construction labor market only grew from approximately 928,600 to 1,300,400 persons (40% in 10 years). In that same period, new residential building starts grew from 526,000 to 1,326,000 annual units (152% increase). Without expanding the labor force or improving productivity, the residential construction sector will continue to struggle to match demand6. To alleviate the demands of the existing workforce, pursuing increased labor productivity is a must. Current studies show remarkable improvement in the last two decades, particularly in multifamily housing construction7. The work of Sveikauskas et al. (2018) demonstrates the need for understanding the interplay between subcontractor and direct labor. Subcontractors account for 44.2% and 74.5% of all single and multifamily housing construction respectively. Perhaps because of that split in division of labor and specialization, productivity in multifamily construction over doubled since 1987, while single family remained relatively stable.
Moving forward, we can advise residential construction firms to pursue organizations and building preferences to maximize productivity. This would not only alleviate constraints by the materials and labor markets, but also help close the housing deficit. Furthermore, it gives them flexibility in their labor planning to avoid unnecessary layoffs and maximize the cost effectiveness of their current workforce.